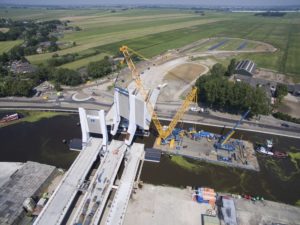
Sarens Group has been involved in a project at Queen Maxima Bridge
Hollandia Infra contacted the Sarens Group around a year ago to discuss a project involving the Queen Maxima Bridge. Crossing the Old Rhine River at Alphen aan den Rijn, Netherlands, the planned new structure included a balanced tail bridge design, where the tails contain counterweights that ensure smooth opening and closing of bridge segments, allowing tall vessels to pass through.
The project called for lifting and positioning the two main balanced tail bridge segments weighing in excess of 280 tonnes (310 tons) from barges on the Old Rhine River.
Adding to the complexity, there was a narrow navigation channel through which barges carrying Sarens’ specialized lifting equipment had to pass. The required crane and supporting equipment would enter the river at Dordrecht, NL, and navigate nearly 50 kilometres upstream to the bridge project site spanning the Old Rhine River. “The top challenge for working on water was the narrow, 11.4 metres (37.4 feet) wide passage in some parts,” said Robin van Oss, project engineer for Sarens.
The Demag CC 3800-1 lattice boom crawler crane offered the right combination of compact footprint and heavy lift capacity required for this job. In addition to the Demag crane, Sarens’s plan called for a 100 tonne (110 ton) capacity mobile crane for lift support, a twin barge configuration and strand jacks. Sarens’ Sarspin device – with its four hydraulic leveling cylinders and up to 600 tonne (660 ton) capacity – would also be integral in helping the CC 3800-1 crane to position the pivoting bridge segments.
To handle the 230 and 280 tonne (253.5 and 310 ton) weight of the two bridge segments, the Sarens plan required the Demag 650 tonne (715 ton) crane to be configured with its Superlift structure to increase crane capacity.
The 30.7 m (100.7 ft) long bridge segments required LSL_2 configuration with 60 m (197 ft) of main boom for the CC 3800-1 crane and 36 m Superlift mast.165 tonne counterweight on the crane’s superstructure , 50 tonne central ballast and 325 tonne on Superlift tray were necessary to give the crane a 347 tonne (382.5-ton) capacity when working at the predetermined fixed 24 m (78.7 ft) radius.
Sarens’ 10-person crew had the crane rigged with main boom, Superlift mast and full counterweight within three days. The car body was maneuvered onto the first barge, while the Superlift tray and maximum counterweight was positioned on the second. Both barges navigated the narrow channel passageway independently of each other.
Sarens’ crew members connected the two barges together and the Superlift counterweight tray to the crane. While a tugboat positioned the two barges carrying the lifting equipment, a separate vessel positioned the enormous balance trap type tail bridge main segment, upended on its wings, next to the crane barge.
It took around four hours to lift the west side bridge segment to height and another two hours for moving the crane barges and load into installation position. Within a final three hours, Sarens’ crew attached the pivoting segment of the bridge to complete the first lift. The entire process was completed in one long day.
The two crane equipment barges were then split apart and repositioned on the east side of the Queen Maxima Bridge. Attachment of the second moveable bridge segment went as smoothly as the first. Within two weeks, segment installation was complete.